These are photos and details of mice
that I saw at the Electronic Design Show recently. Please
excuse any errors.
This is Chris Pickering's
Mouseratti. This has run times under 5 seconds in
the school's standard class. It is currently detuned for
exhibition purposes but is still pretty quick!
This is a big Meccano-based mouse that
was on display at the EDS show at the NEC. It is reliable
but slow(ish) (everything is relative!). I think it was
built at Woodroffe school.
This is John Pickering's
Drive-by-Wire. This is a tiny mouse that ran at
the EDS show. It was good enough to scare us into some
rapid development at the competition.!
The design is simple but certainly not
crude. The "intelligence" is supplied by two
microswitches. These are operated by the long,
critically-shaped feeler wire via a cam. There is an
additional contact made between the feeler and an
adjustable wire to give zero-hysteresis switching for
following the wall during a cell. The microswitches deal
with the rapid turns needed at corners.
The wheels are taken from a slot-car
racer and are very grippy.
This is Swallow Systems' DOT.
Somewhat quicker than a DASH, it won the
wall-following competition at the Electronic Design
Solutions show. It uses one of our drive trains, three
Hamamatsu sensors (two area-coverage versions, one
single-LED version), and an AVR 2313 processor. The motor
speed setting is done with an array of trimmers and it
uses a relay to reverse the right-hand motor when
necessary. There is a power FET across the left-hand
motor for braking.
The software is very crude; all it
does is read the three sensor inputs, look up which
trimmers to select and whether to reverse the motor or
apply a brake. There are about 30 lines of
code.
The limiting factor on performance is,
as ever, tyre grip and braking.
The system is run from 5 AAA
NiCds.
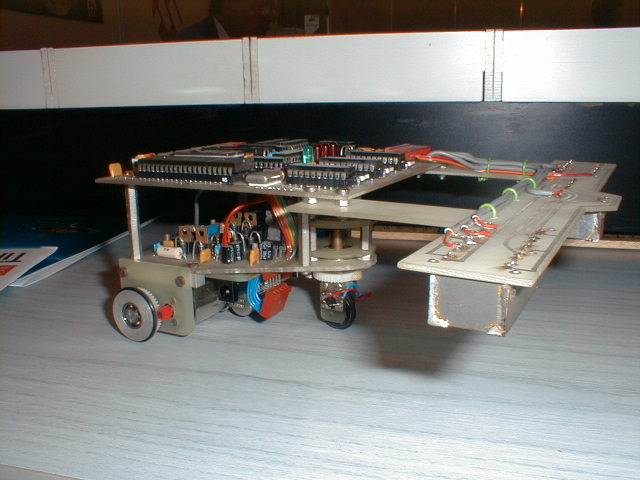
These are two of Dave Woodfield's
mice. One is Voyager and the other is Enterprise. I am
not sure which is which but I think the bottom one
is Enterprise.
The top one has about 500 hours work
in it; no wonder that Dave is probably the most
successful mouse builder in Britain. It has very powerful
stepper motors. He told me that they cost him about
£80 each. The top board has an FPGA to control the
steppers and the bottom board has the processor for
maze-solving etc.
The lower picture shows one of his
tricycle mice. One of the problems that everyone has with
this style of mouse is moving the steering quickly
enough. Many mice use radio control servos for steering
but the faster competitors use very special servos or
modify them to give much quicker response. When I checked
with our local model shop, I found that these type of
servos take about 100ms to turn 60 degrees. At nationally
competitive speeds of 1 metre/sec that corresponds to 10
centimetres! This is a big problem when the gap you are
aiming at is only 16 centimetres wide.